Ground Granulated Blastfurnace Slag
This material is manufactured to comply with the requirement of EN 15167-1 : 2006 and exceeds the minimum strength and fineness requirement by a considerable margin.
This product is kitemarked by BSI to BS EN 15167-1 and our License Number is KM 58897.
DCL Certification for EN 15167-1 and ASTM989M
This material is produced by grinding dried Granulated Slag in a closed circuit milling system to a surface area of ~380m2/kg. This Granulated Slag is the same material used to produce Blastfurnace cement.
The quality control of Ground Granulated Blastfurnace Slag manufacture is in five stages:
Purchase of slag from a supplier with a long history of producing a consistent and quality product. A Manufacturer’s Test Certificate is obtained before purchasing slag.
Analysis of the slag at the factory for chemical composition using X-Ray Fluorescence, and glass content using X-Ray Diffraction.
Control of drying of the slag to produce Granulated Blastfurnace Slag with consistent moisture content.
Quality control during milling, by changes in mill running parameters to control surface area and particle size distribution.
Chemical and Physical tests are carried out on the finished product:
1. Full chemical analysis in accordance with the requirements of EN 15167-1 2006.
2. Full range of physical test in accordance with EN 15167-1 2006 including compressive strength test on a combination of 50% Ground Granulated Blastfurnace Slag and 50% Portland Cement.
Samples of Ground Granulated Blastfurnace Slag are sent, periodically, to an independent laboratory for testing.
USE
This product is intended to be used in concrete either as a component of composite cements such as Blastfurnace Cement/High Slag Blastfurnace Cement or as a direct addition to the concrete mix by the concrete producer.
BS 8110 and BS 5328 have made it clear that there is no distinction, on technical grounds, between manufactured composite cements and blending of the separate components in the concrete mixer. Unless there are special reasons it would be normal to permit either method to be selected by the contractor.
An important requirement of BS 8110 and BS 5328 is that, for a combination to be classed as a cement, it must satisfy the standard for the composite cement in respect of proportions and properties. In the case of the interground composite cement, the responsibility for certification lies with the cement producer. In the case of combinations blended at the mixer, this responsibility rests with the concrete producer. In either case compliance certificates should be supplied for the composite cement, or for the constituents blended in the mixer.
When Ground Granulated Blastfurnace Slag is blended with cement or added to the concrete mixer the amount of soluble SO3 and C3A is reduced in proportion to the slag added. While we are not aware of any difficulties in setting times or admixture performance we advise comprehensive mix trials especially at high slag replacement levels to check workability.
The use of cement from a single source with a consistent C3A, alkali, free lime and fineness is recommended to minimize concrete variability.
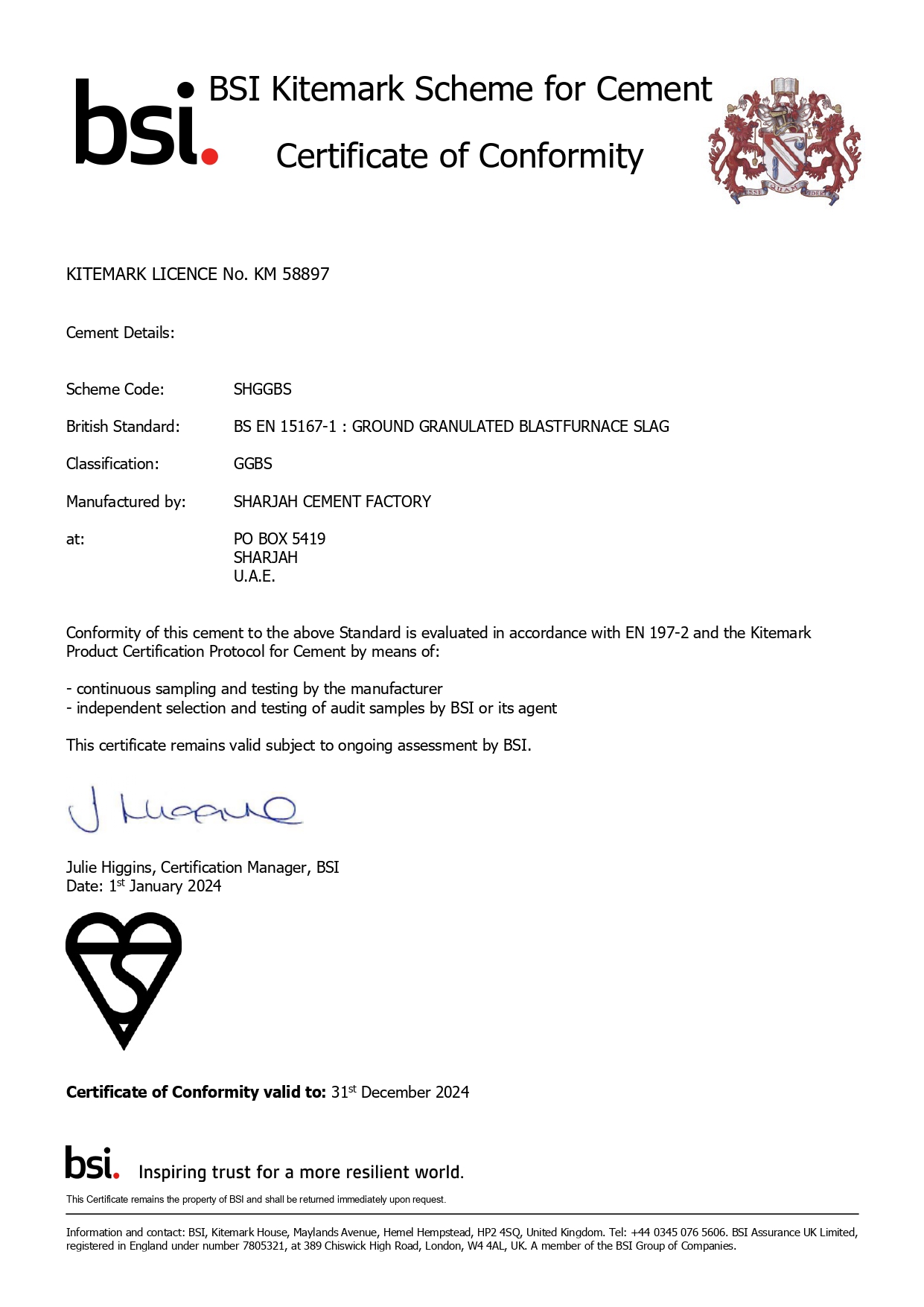